Blogs

Why Do We Perform Salt Spray Corrosion Testing and
Updated at: 2025-03-24 06:31:19
Jung (Corrosion) is an important challenge in various industries, especially in motor vehicles, aero... Read More

Why Salt Spray Testing is Essential for Metal Coat
Updated at: 2025-03-12 10:22:56
In today's industrial world, durability and longevity are important for metal coating and motor vehi... Read More

Industries Benefiting from Salt Spray Chambers for
Updated at: 2025-03-07 06:04:18
Corrosion is a great concern for industries that depend on metals and coatings to ensure the durabil... Read More

How to Operate a Cass Cum Salt Spray Chamber Effec
Updated at: 2025-02-26 09:11:11
A salt spray test is an important method for evaluating the test material and corrosion resistance t... Read More
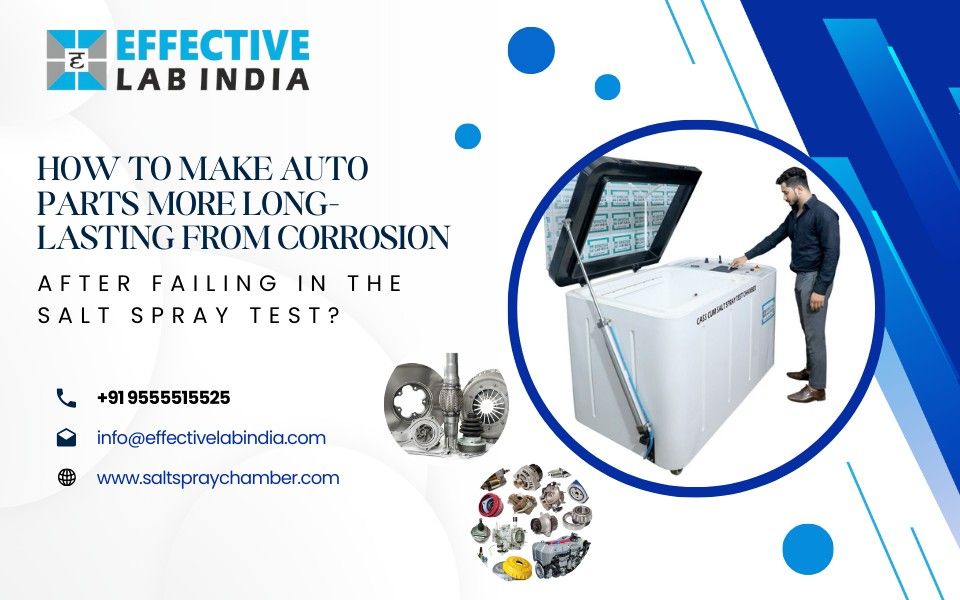
How to Make Auto Parts More Long-Lasting from Corr
Updated at: 2025-02-20 05:43:55
Corrosion is a serious challenge for car parts, especially in contact with a stiff environment. Many... Read More
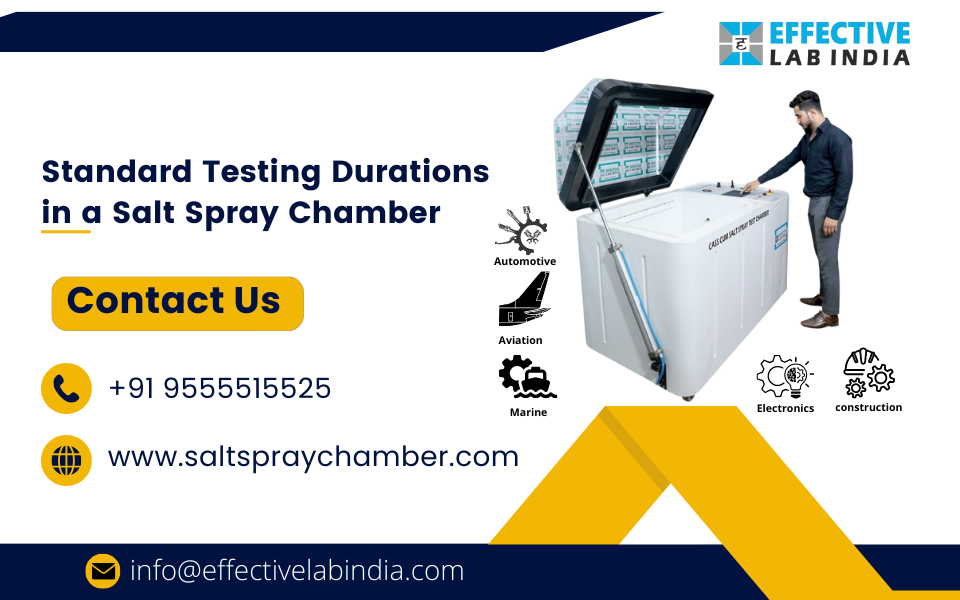
Standard Testing Durations in a Salt Spray Chamber
Updated at: 2025-02-15 06:28:58
IntroductionIn industries where metal components are used, corrosion resistance is an important fact... Read More
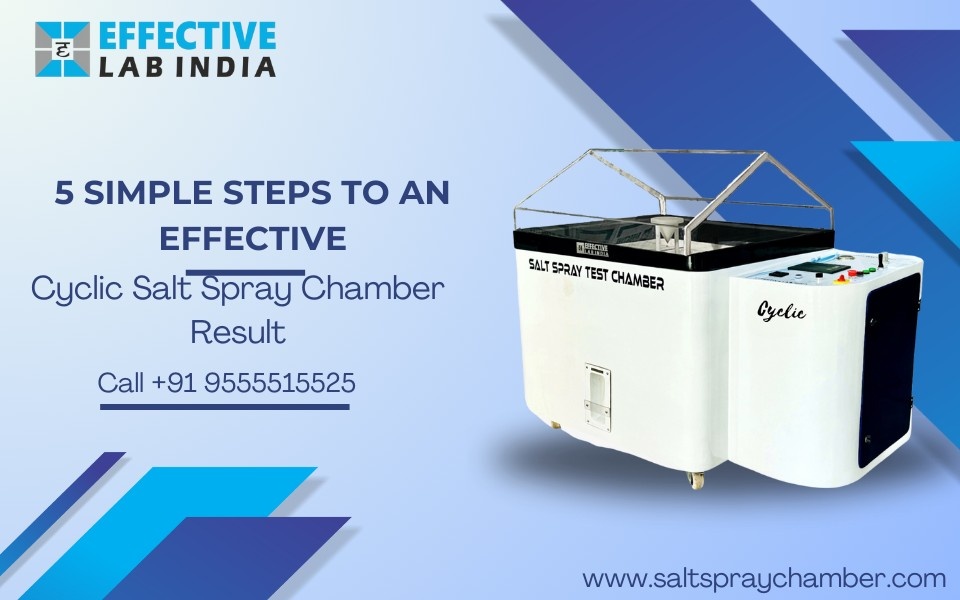
5 Simple Steps To An Effective Cyclic Salt Spray C
Updated at: 2025-02-13 05:33:11
One essential technique for assessing a material or coating's ability to withstand corrosion is cycl... Read More
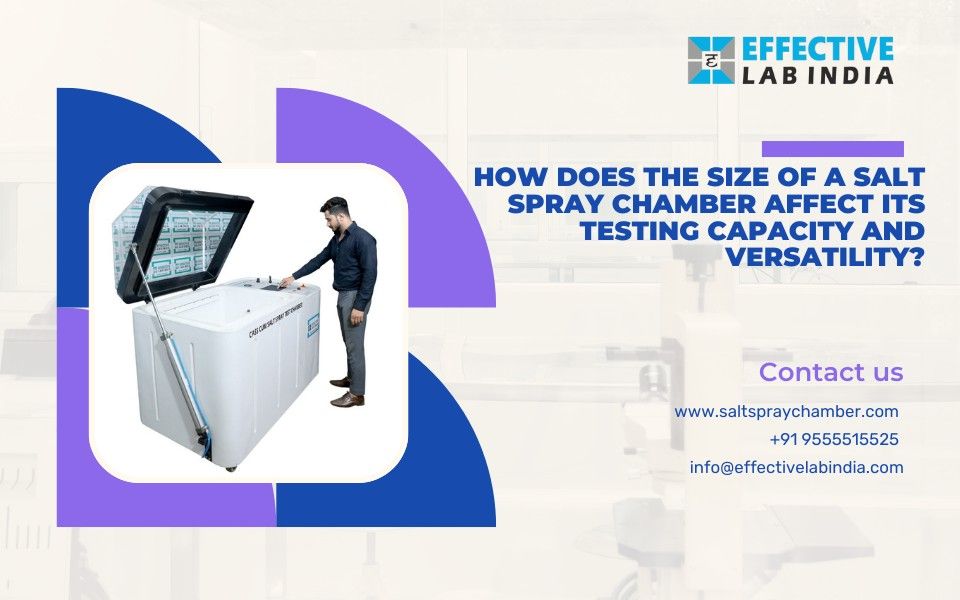
How Does the Size of a Salt Spray Chamber Affect I
Updated at: 2025-02-07 09:10:39
When evaluating the corrosion resistance of materials, coatings, and components, salt spray testing ... Read More
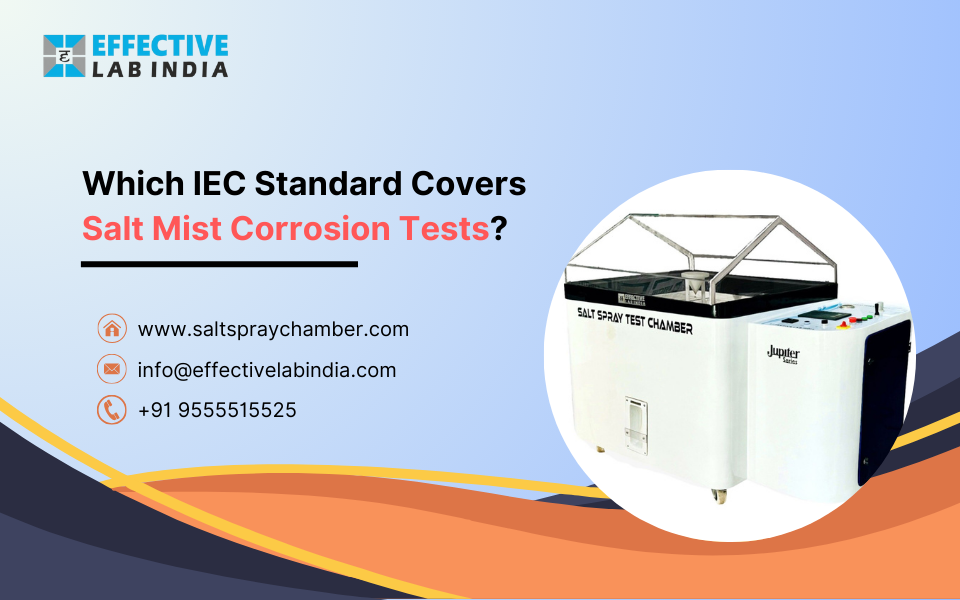
Which IEC Standard Covers Salt Mist Corrosion Test
Updated at: 2025-02-05 06:32:12
Salt mist corrosion tests are essential for assessing a material's or coating's resistance to corros... Read More

Salt Spray Fog Test for Corrosion Testing of Carbi
Updated at: 2025-01-30 09:02:12
One of the most important factors in determining the longevity of materials used in a variety of ind... Read More
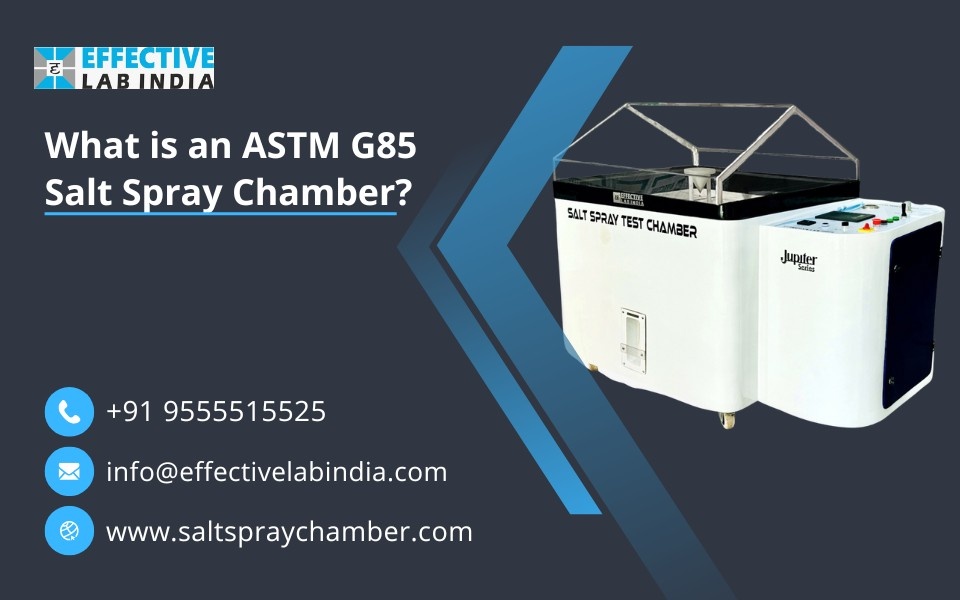
What is an ASTM G85 Salt Spray Chamber?
Updated at: 2025-01-28 06:47:16
A specialized tool called an ASTM G85 Salt Spray Chamber is needed for sophisticated corrosion testi... Read More
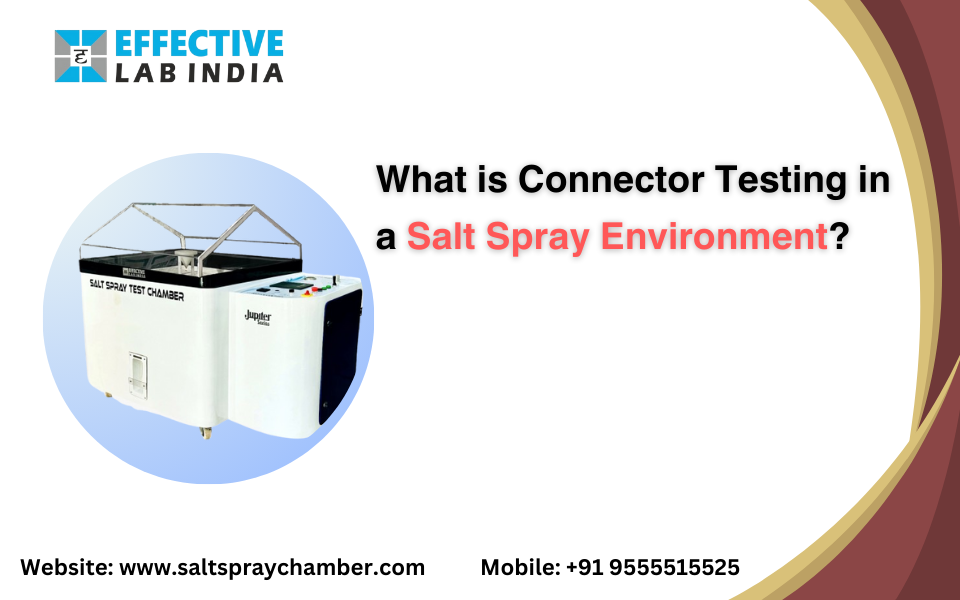
What is Connector Testing in a Salt Spray Environm
Updated at: 2025-01-22 11:48:12
Connector testing in a salt spray environment is an essential procedure for assessing the robustness... Read More

Key Features to Look for in a Salt Spray Test Cham
Updated at: 2025-01-16 07:02:54
Metals and other materials are gradually corroded by corrosion, which is a quiet destroyer. Industri... Read More
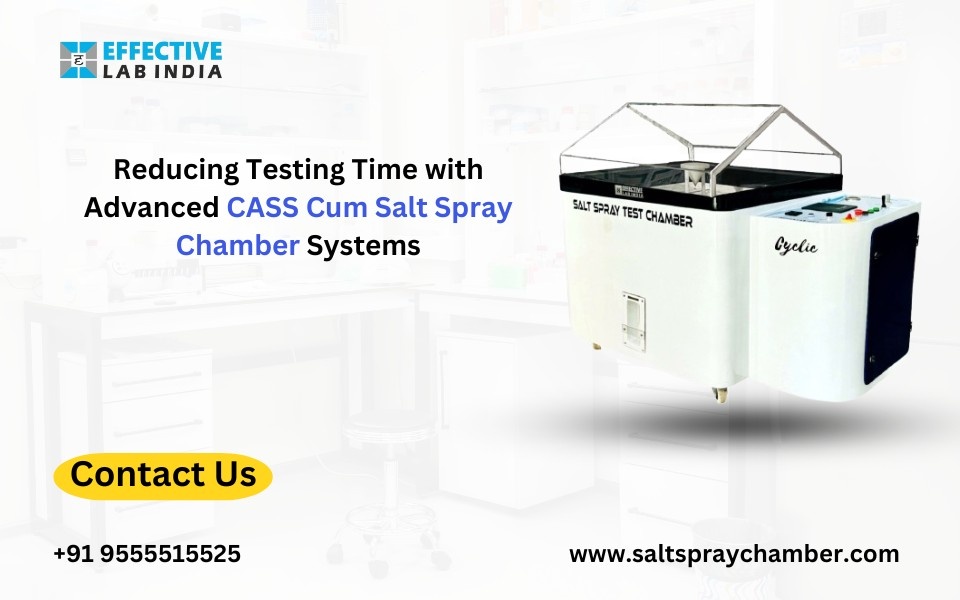
Reducing Testing Time with Advanced CASS Cum Salt
Updated at: 2025-01-13 06:37:43
A crucial stage in the competitive world of creation and manufacturing is quality assurance. Corrosi... Read More

Simulating Corrosive Environments in Salt Spray Ch
Updated at: 2025-01-08 07:22:07
Ensuring the longevity and dependability of materials is crucial in today's demanding industry. One ... Read More

Applications of CASS Cum Salt Spray Chambers in Au
Updated at: 2024-12-31 08:13:51
Testing and analysis are important in industries such as aerospace and automotive where product qual... Read More

How Does a Salt Spray Chamber Work? Working Princi
Updated at: 2024-12-30 09:26:47
The salt spray chamber, which is sometimes referred to as a salt fog test chamber, is the essential ... Read More
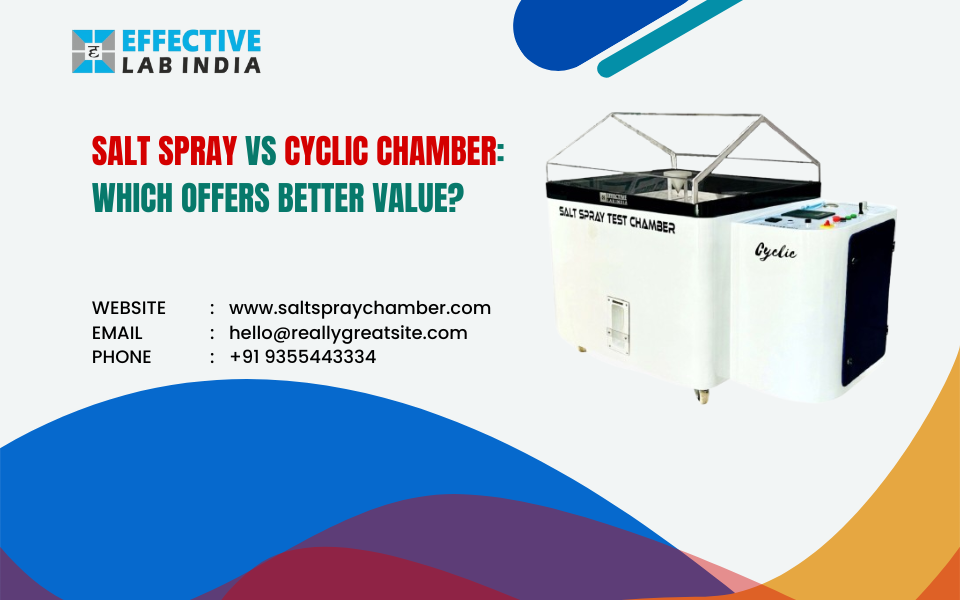
Salt Spray vs Cyclic Chamber: Which Offers Better
Updated at: 2024-12-27 08:05:18
In sectors like automotive and aerospace, corrosion testing is essential for making sure that coatin... Read More

Top Budget Salt Spray Test Chamber Models in 2025
Updated at: 2024-12-23 07:38:59
Salt spray test chambers are essential for industries including manufacturing, aerospace, and automo... Read More

Top 10 Features to Look for When Choosing a CASS T
Updated at: 2024-12-23 05:53:22
Salt spray test chambers, also known as CASS test chambers, are essential equipment for construction... Read More
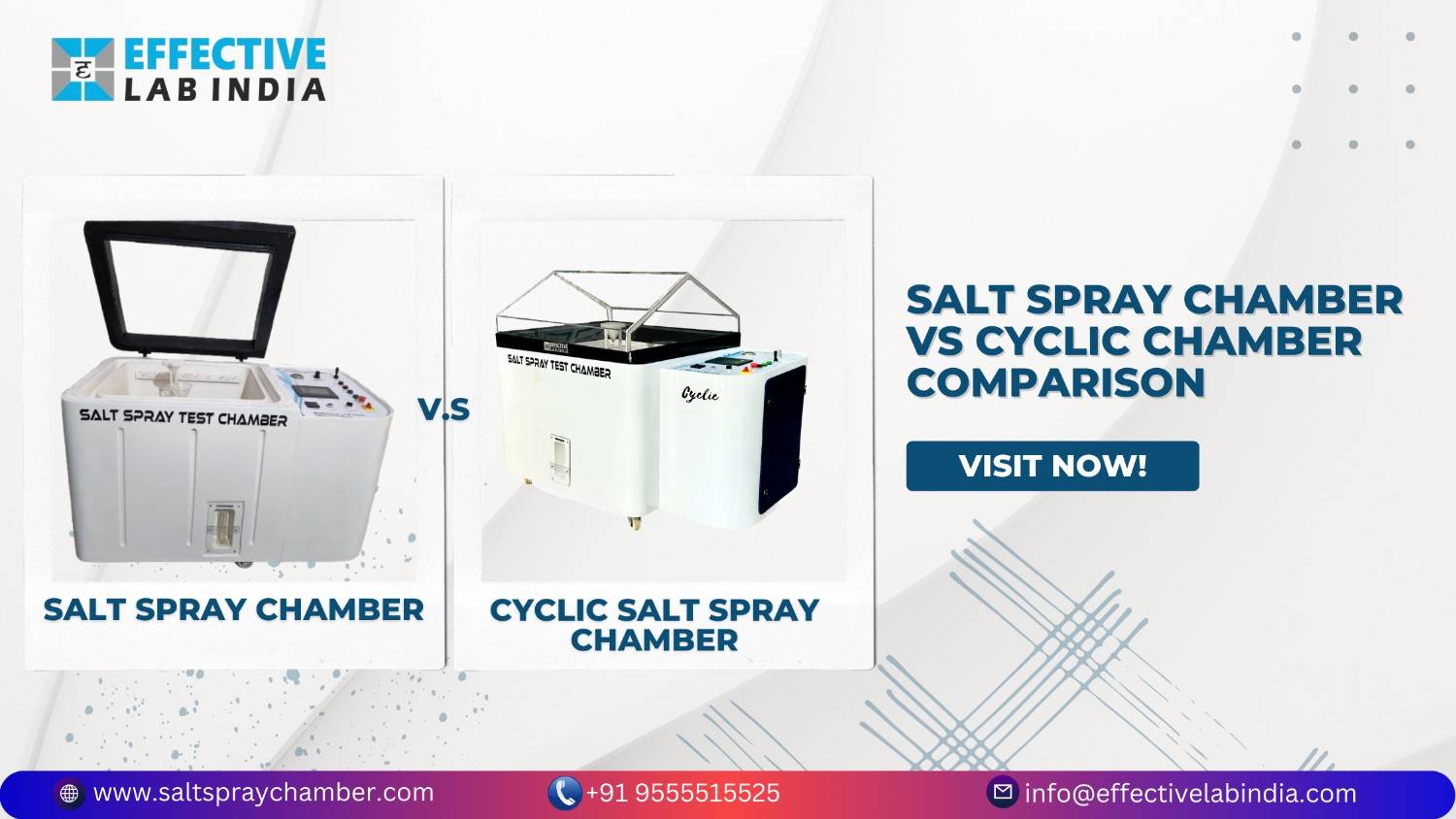
Salt Spray Chamber vs Cyclic Chamber Comparison |
Updated at: 2024-12-20 07:20:28
The argument between salt spray chambers and cyclic salt spray chambers is continuing strong in the ... Read More

What Are the Salt Spray Test Requirements for Scre
Updated at: 2024-12-18 08:54:28
An important step in the quality assurance process is to conduct salt spray testing to verify the co... Read More
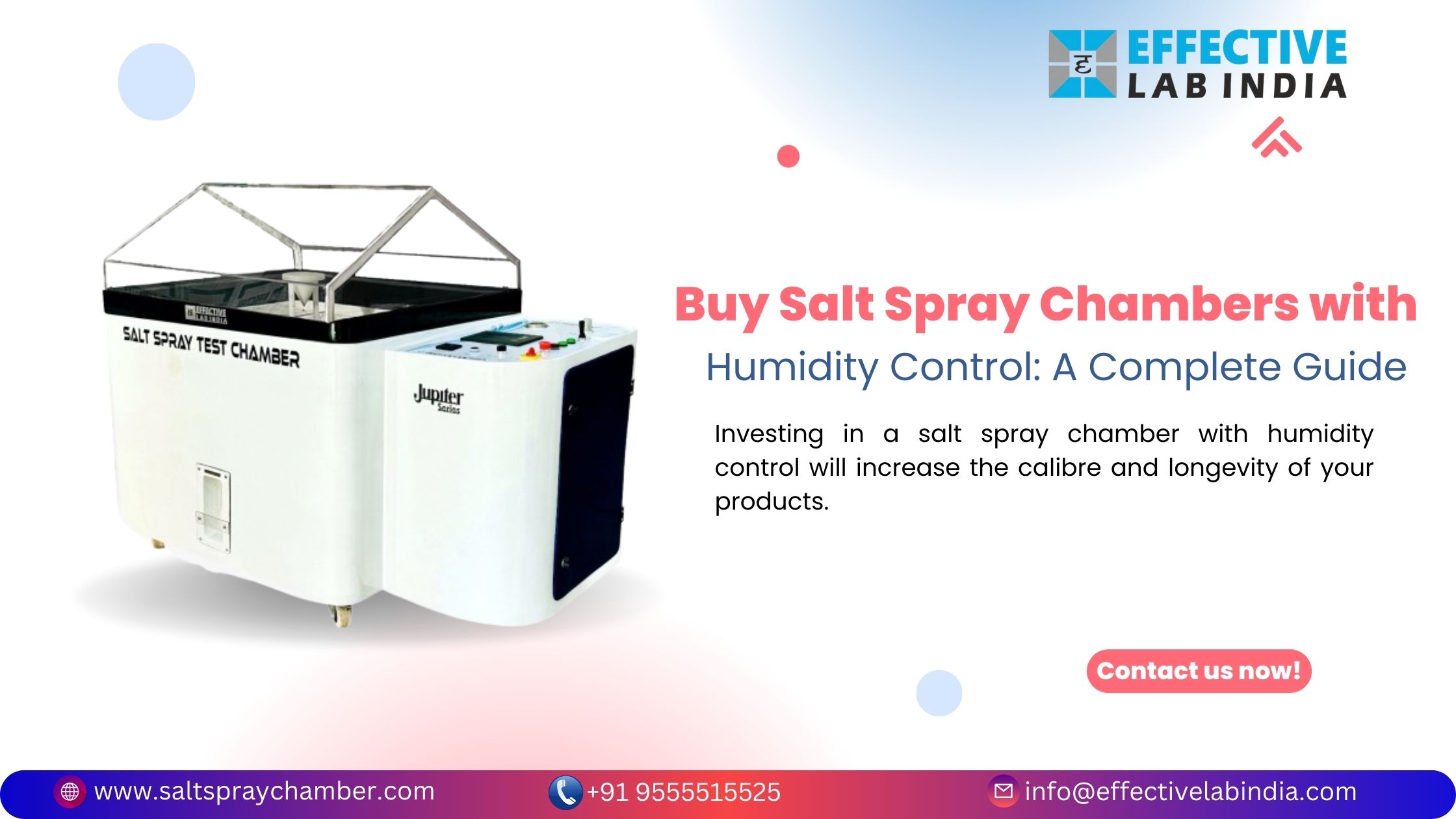
Buy Salt Spray Chambers with Humidity Control: A C
Updated at: 2024-12-17 05:36:46
If you’re looking for a salt spray chamber with humidity control, you probably know how important ... Read More

Understanding Paints & Coatings Testing with Salt
Updated at: 2024-12-12 09:56:21
Proper inspection techniques are essential to ensure the durability and effectiveness of paints and ... Read More
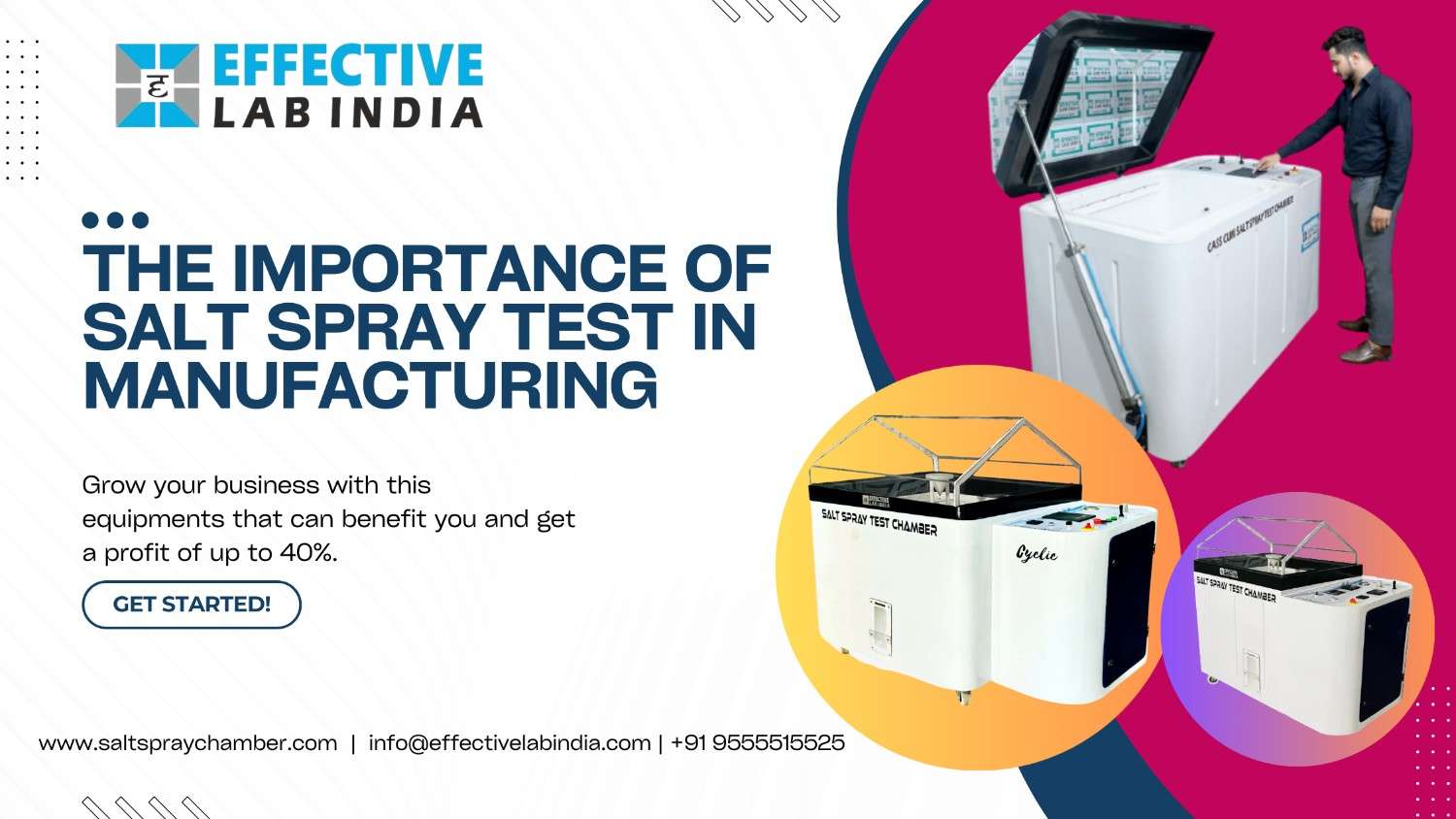
The Importance of Salt Spray Test in Manufacturing
Updated at: 2024-12-09 06:36:53
In today’s competitive construction industry, quality is paramount. Whether you’re in th... Read More

Accelerate Salt Spray Testing with the Cass Cum Sa
Updated at: 2024-12-06 09:16:19
Where the durability and corrosion resistance of the material are the top priority, salt spray testi... Read More

Why Salt Spray Chambers are Essential for Corrosio
Updated at: 2024-12-04 07:18:38
Corrosion is a huge problem for enterprises around the world because it damages metals and materials... Read More

Impact of Temperature and Humidity on Salt Spray T
Updated at: 2024-12-02 07:23:04
A common method for assessing a material or coating's resistance to corrosion is salt spray testing.... Read More

Testing Metal Paints & Coatings with Salt Spray Ch
Updated at: 2024-11-29 12:03:03
Paints and coatings are essential for shielding metals from rust and corrosion. However, how can we ... Read More

What are the top most popular corrosion tests?
Updated at: 2024-11-25 10:08:29
Environmental factors such as moisture, temperature, and chemical reactions ultimately lead to corro... Read More

Exploring Alternatives to Salt Spray Testing Choos
Updated at: 2024-11-22 06:50:12
One common technique for evaluating corrosion resistance is salt spray testing. Other approaches, th... Read More

Explore the Key Features of High-Performance Salt
Updated at: 2024-11-19 09:29:26
A corrosion test is needed to assess the durability of a company's material items and products. A ke... Read More

7 Essential Features of a Quality Cyclic Corrosion
Updated at: 2024-11-16 06:48:10
Corrosion is a natural process that can have a big impact on the performance and life of a product. ... Read More
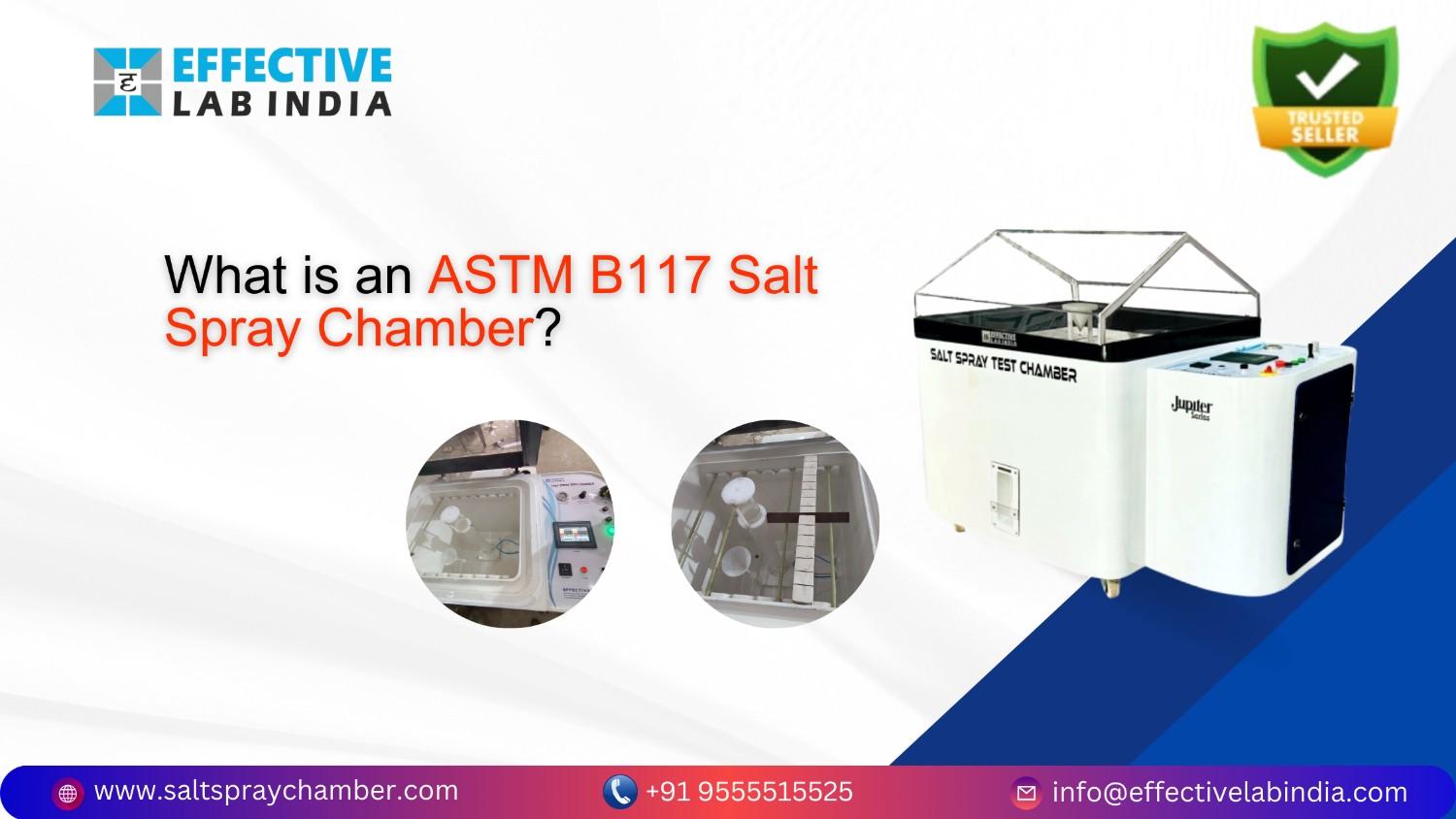
What is an ASTM B117 Salt Spray Chamber?
Updated at: 2024-11-14 09:03:40
Introduction to Salt Spray Testing For many products, corrosion is the silent enemy. Everything exp... Read More
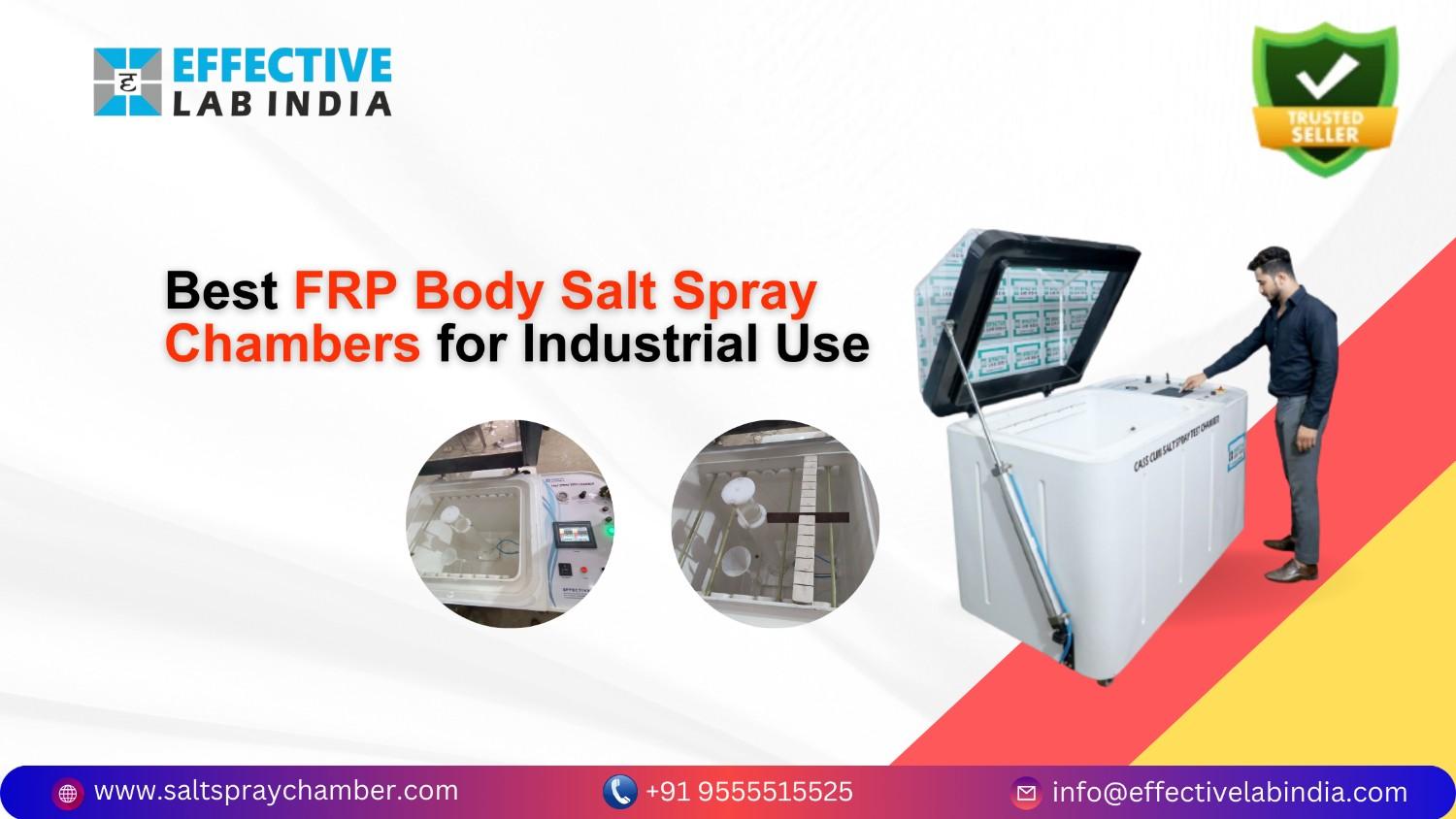
Best FRP Body Salt Spray Chambers for Industrial U
Updated at: 2024-11-12 06:31:02
Salt sprays are essential in industrial tools, materials, and metal alloy testing, especially for co... Read More
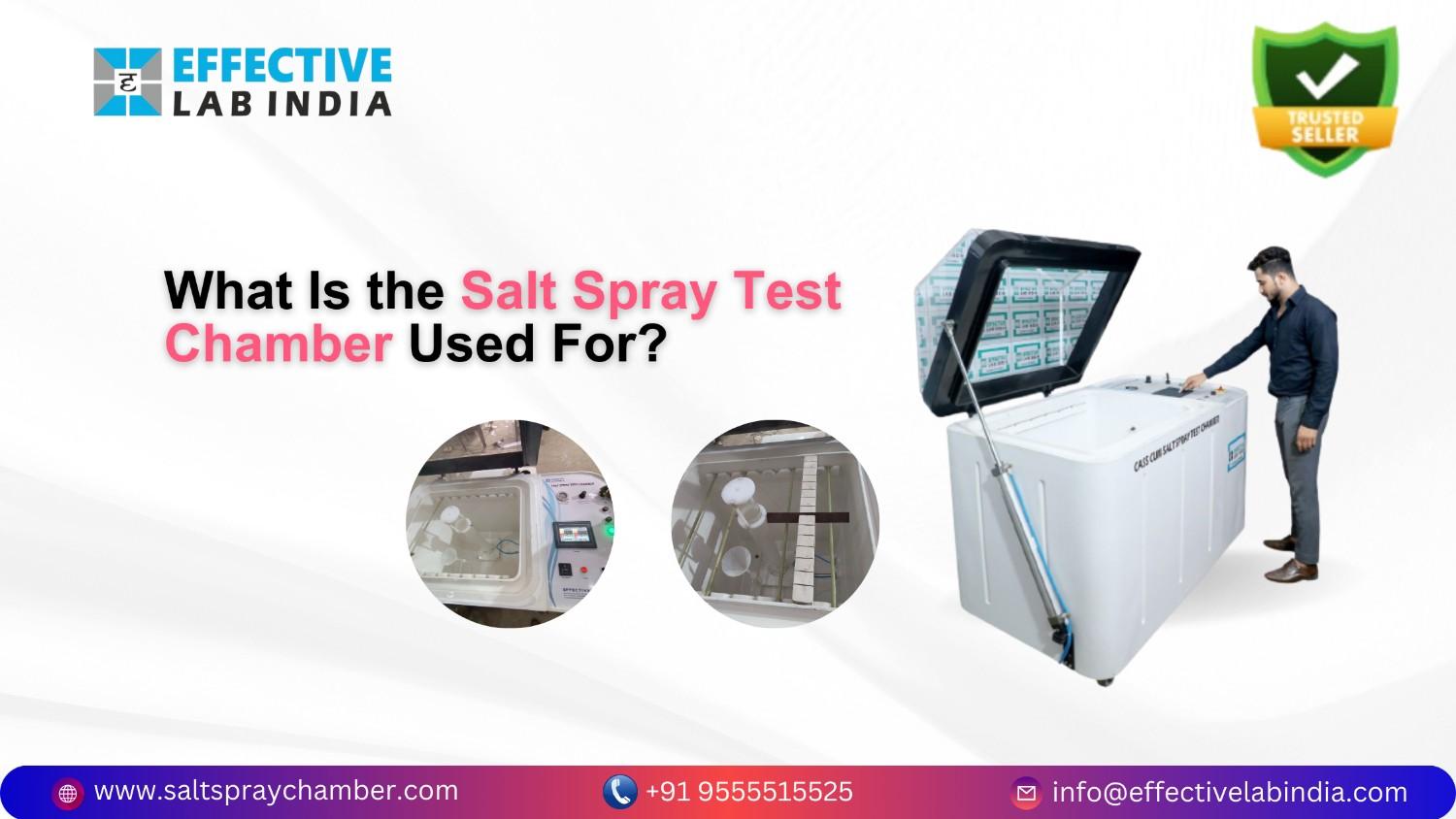
What Is the Salt Spray Test Chamber Used For?
Updated at: 2024-11-09 06:19:01
Manufacturing delays are key in industries ranging from automotive to electronics. Corrosion can aff... Read More

Top Automated Salt Spray Chambers to Buy in 2025
Updated at: 2024-11-08 08:41:00
Salt spray testing is important when evaluating the corrosion resistance of materials, coatings, and... Read More

What Is the Salt Spray Test Chamber ASTM B 117 and
Updated at: 2024-11-07 06:57:39
Have you ever wondered how materials can withstand the most extreme conditions? Salt spray tests can... Read More

Salt Spray Testing Solutions for Pipes and Valves
Updated at: 2024-11-05 06:25:33
Introduction to Salt Spray Testing for Pipes and ValvesSalt spray testing is becoming an essential t... Read More
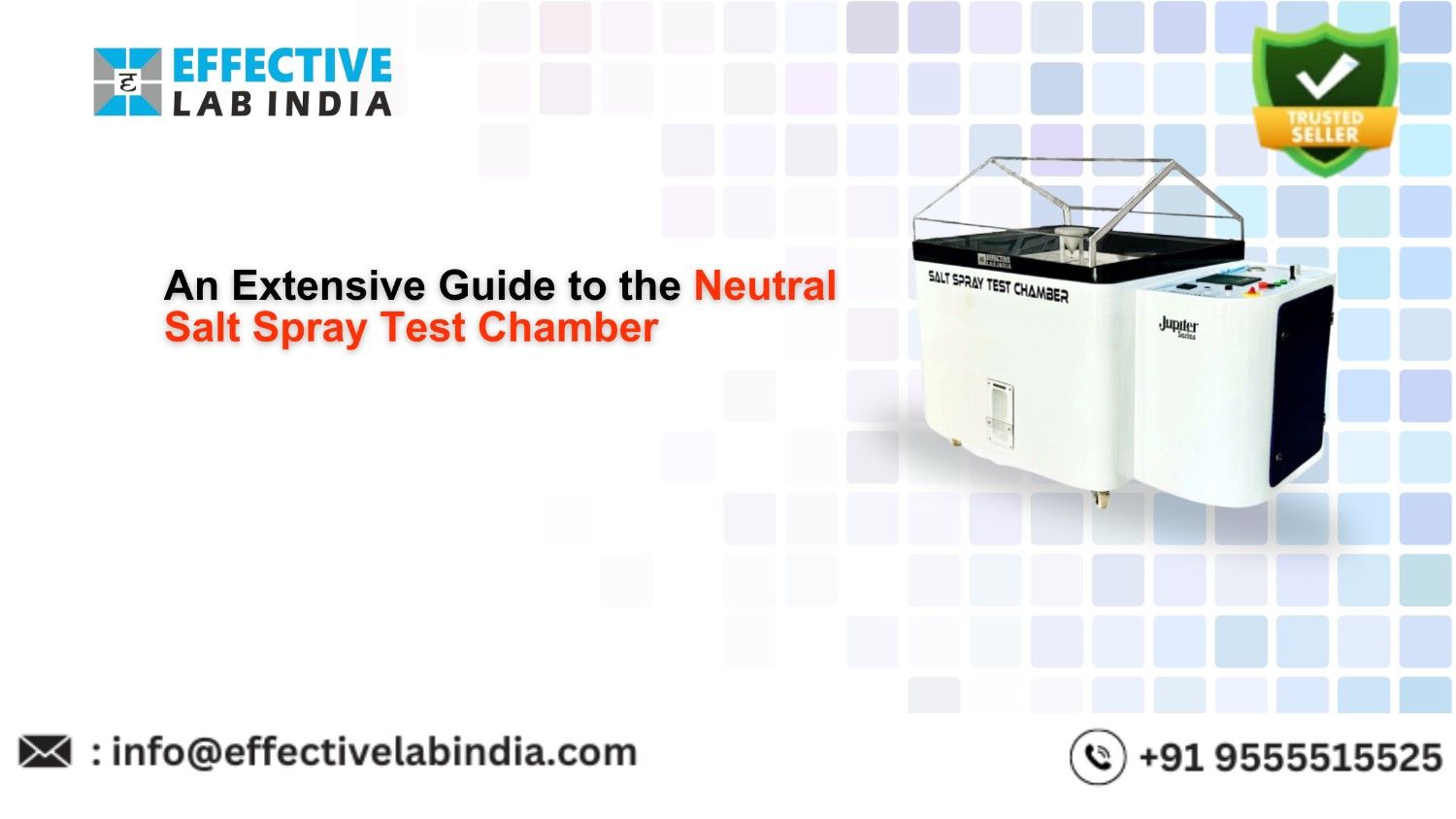
An Extensive Guide to the Neutral Salt Spray Test
Updated at: 2024-11-02 06:46:52
The durability and safety of materials and products may be significantly impacted by corrosion, whic... Read More
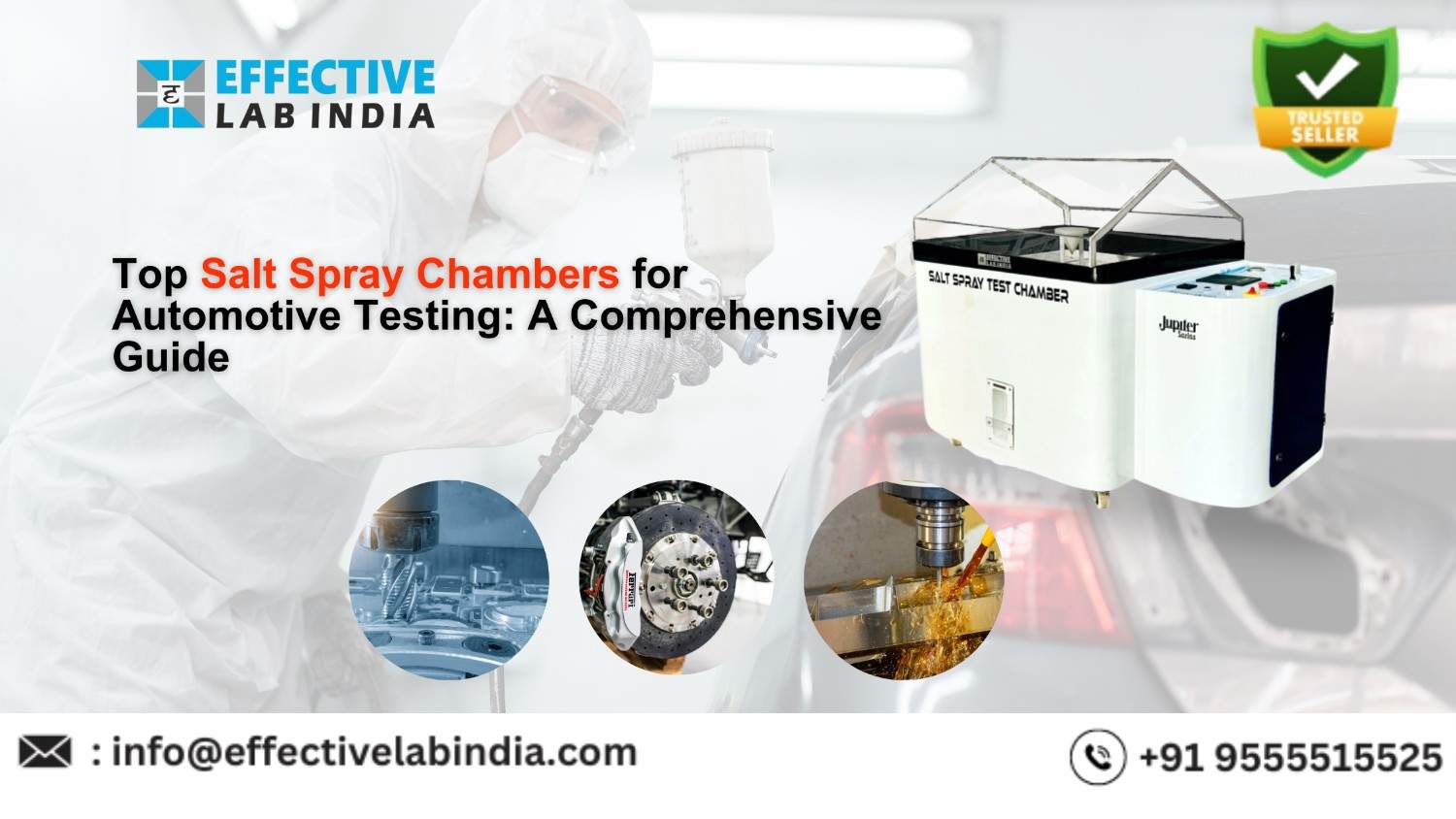
Top Salt Spray Chambers for Automotive Testing: A
Updated at: 2024-10-28 07:00:23
In the automotive industry, where components face relentless exposure to harsh environmental conditi... Read More

Why Do Electronic Products Need Salt Spray Corrosi
Updated at: 2024-10-26 07:38:51
Longevity is crucial for electrical products. We think that our electronic equipment and products wi... Read More

Cyclic vs CASS Salt Spray Chamber: Key Differences
Updated at: 2024-10-24 07:50:19
Salt spray chambers are important when testing the corrosion resistance of coatings and materials. C... Read More
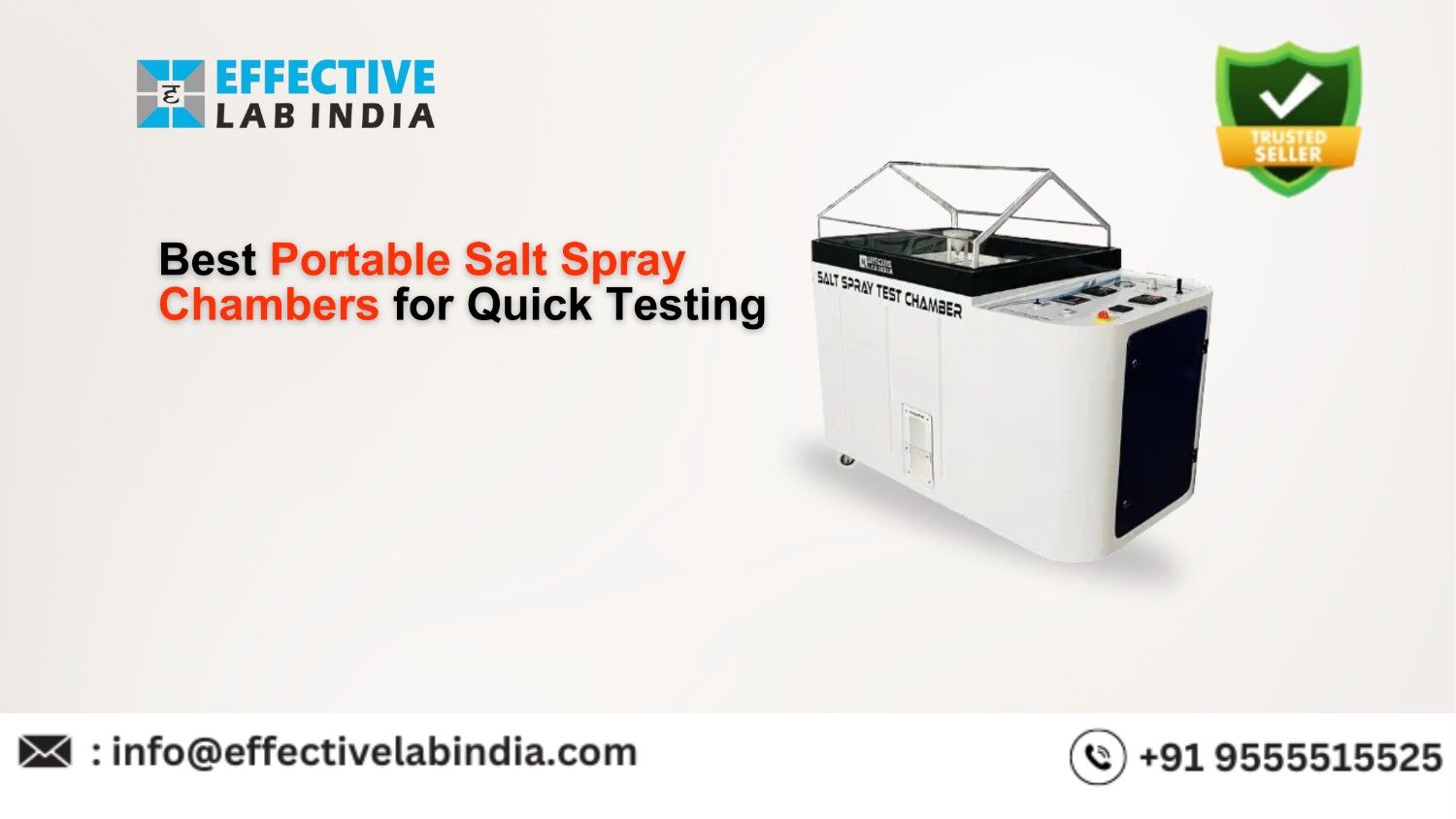
Best Portable Salt Spray Chambers for Quick Testin
Updated at: 2024-10-23 07:32:46
In the modern world of material science, ensuring product durability and longevity is very important... Read More
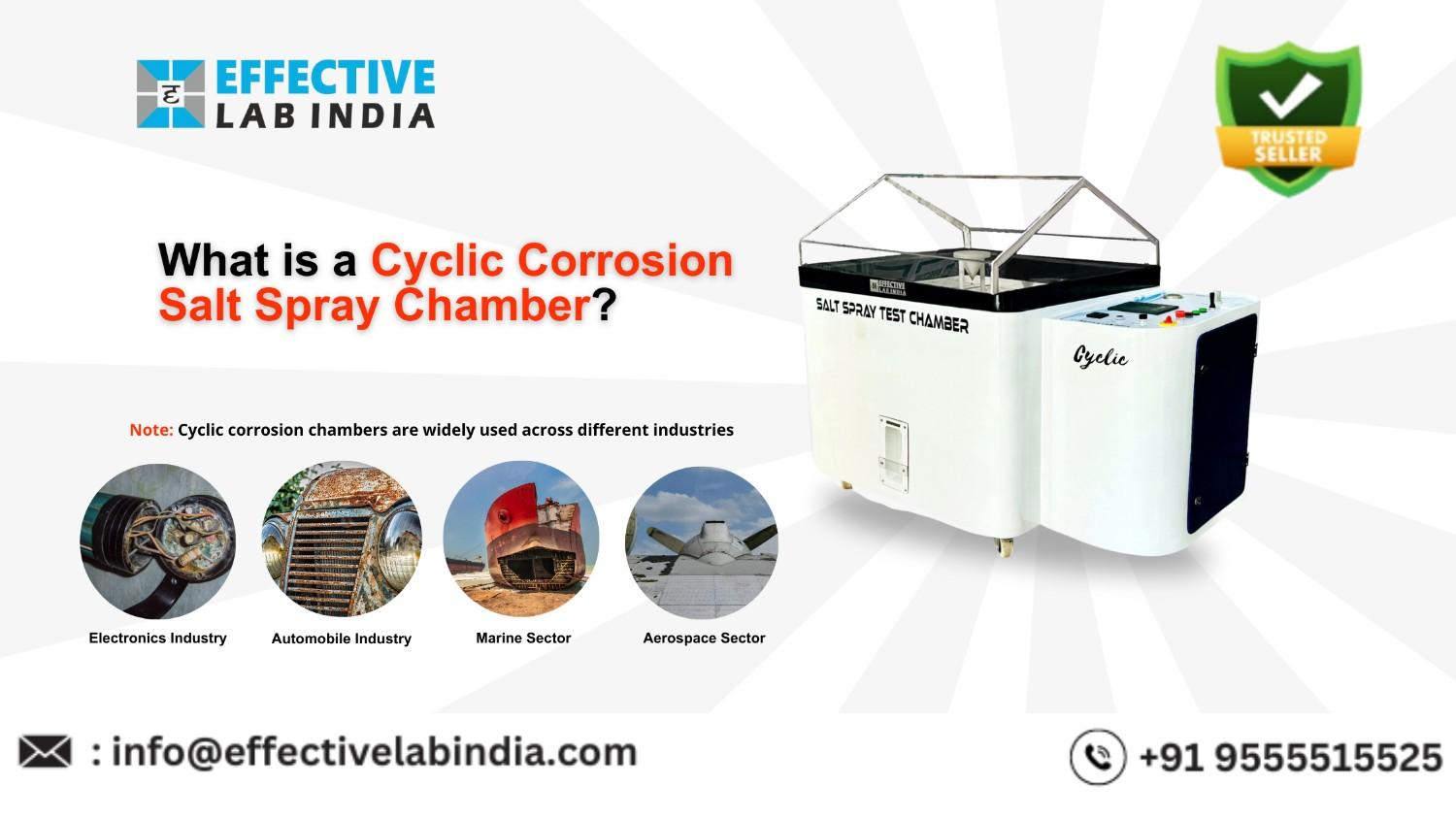
What is a Cyclic Corrosion Salt Spray Chamber?
Updated at: 2024-10-22 07:41:33
Introduction:When working with materials you encounter in harsh environments—like metal, paint... Read More

Key Benefits of Salt Spray Testing Labs for Corros
Updated at: 2024-10-21 09:26:27
Metals and coatings suffer silently from corrosion, which erodes materials over time. For the longev... Read More
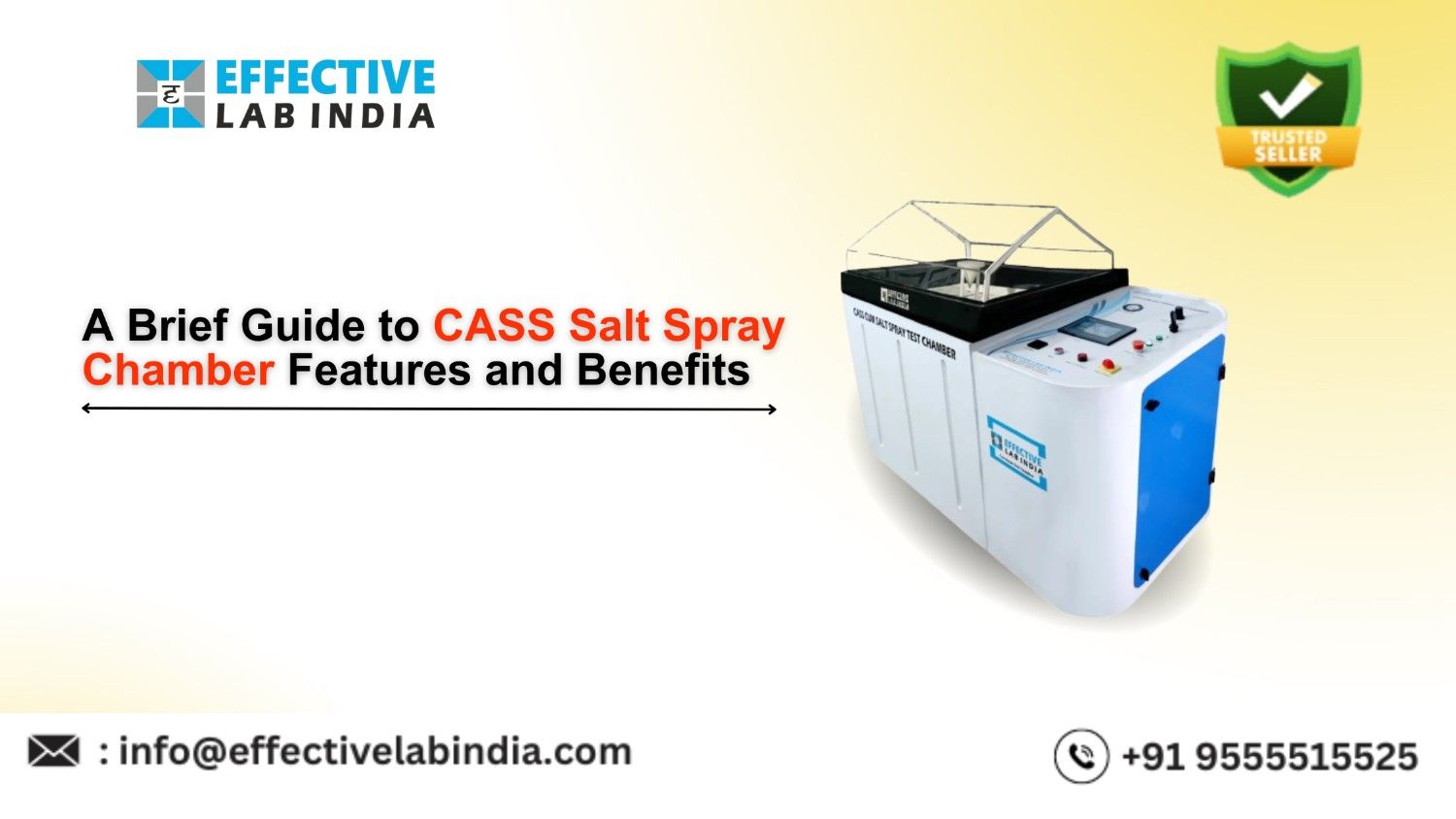
A Brief Guide to CASS Salt Spray Chamber Features
Updated at: 2024-10-19 09:44:16
For components in the metal manufacturing, automotive, and aerospace industries, corrosion testing i... Read More

Salt Spray Chambers Prices & Budget-Friendly Optio
Updated at: 2024-10-18 07:09:23
Salt spray chambers are indispensable tools for testing corrosion resistance, especially for industr... Read More
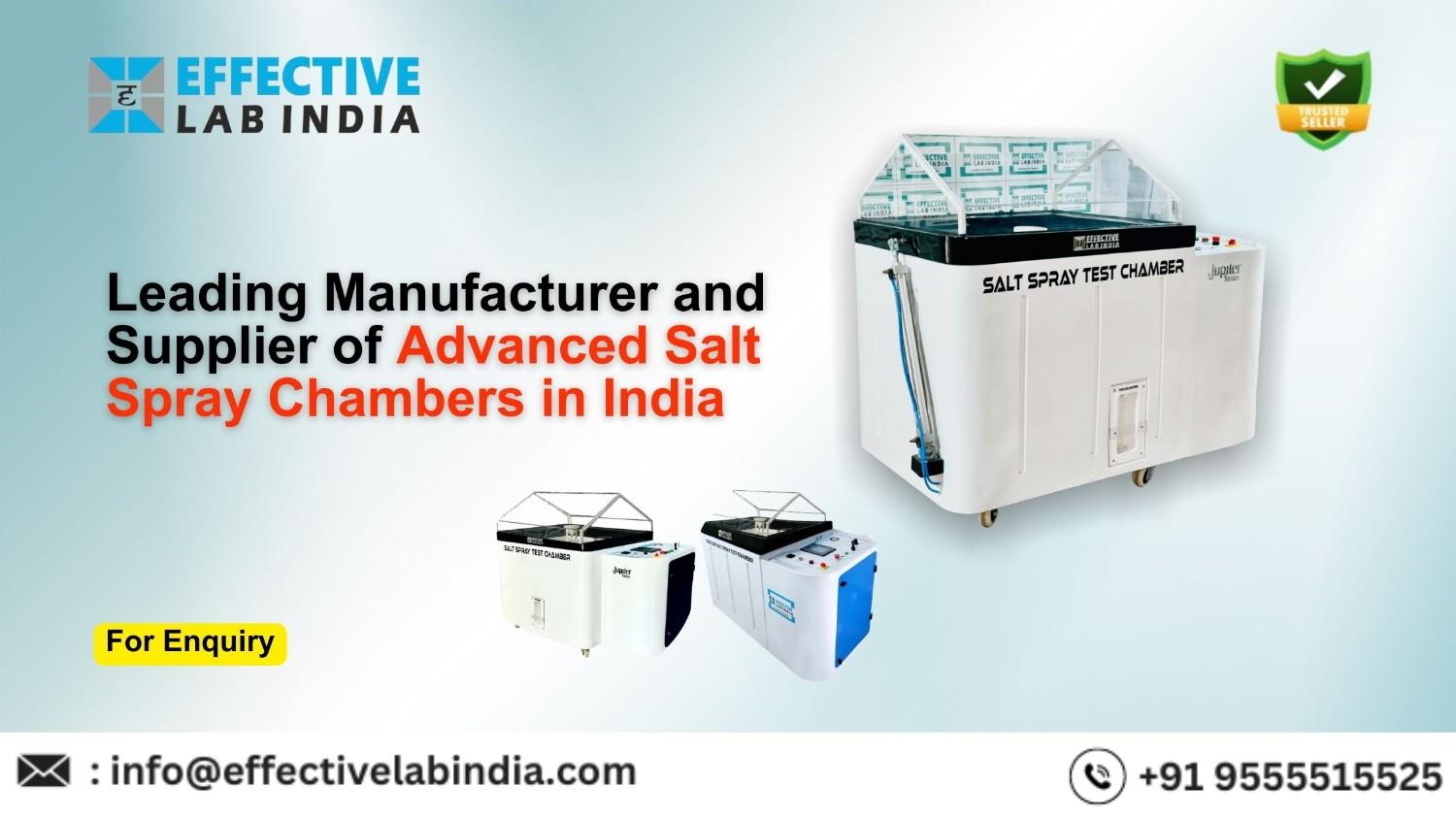
Leading Manufacturer and Supplier of Advanced Salt
Updated at: 2024-10-17 06:51:02
Salt spray chambers are used for corrosion testing. These cabinets imitate harsh environmental condi... Read More

What is a Salt Spray Test Chamber and Why is it Im
Updated at: 2024-10-15 07:16:12
Introduction Have you ever wondered how manufacturers make sure that their products can withstand c... Read More

Establishing the Relation Between Salt Spray Test
Updated at: 2024-10-11 06:15:09
The salt spray test effectively evaluates the corrosion resistance of a material. This is important ... Read More
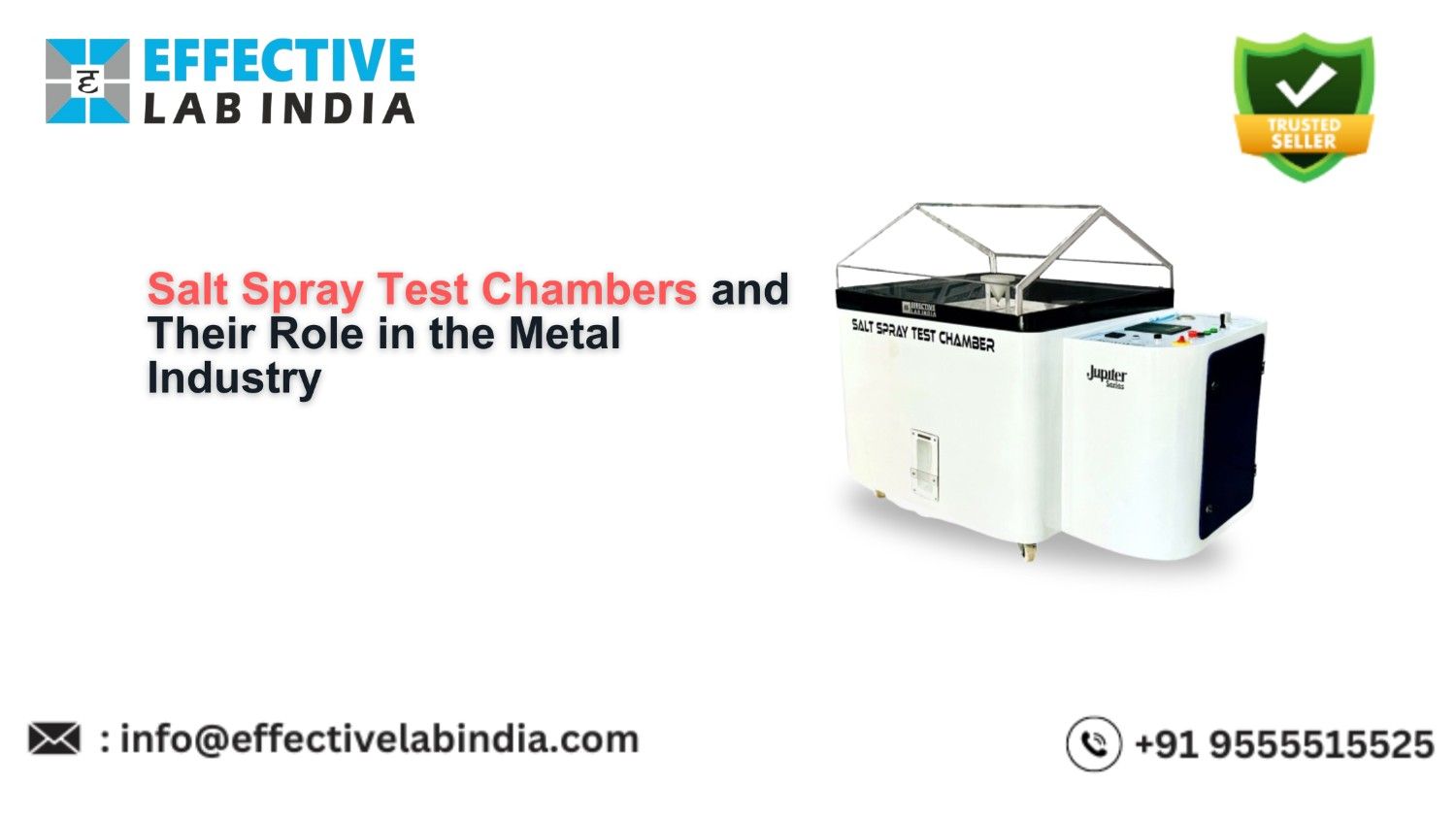
Salt Spray Test Chambers and Their Role in the Met
Updated at: 2024-10-09 06:00:33
Many businesses suffer damage by corrosion, but the metal manufacturing industry is particularly at ... Read More

A Guide to Properly Handling Samples for the Salt
Updated at: 2024-10-07 07:33:59
Electroplating is an important process in industries from automotive to aerospace, providing corrosi... Read More

Examine Your Sample Conditioning in a Salt-Laden E
Updated at: 2024-10-04 07:05:13
In the world of testing, it is important to ensure that the product can withstand harsh environmenta... Read More
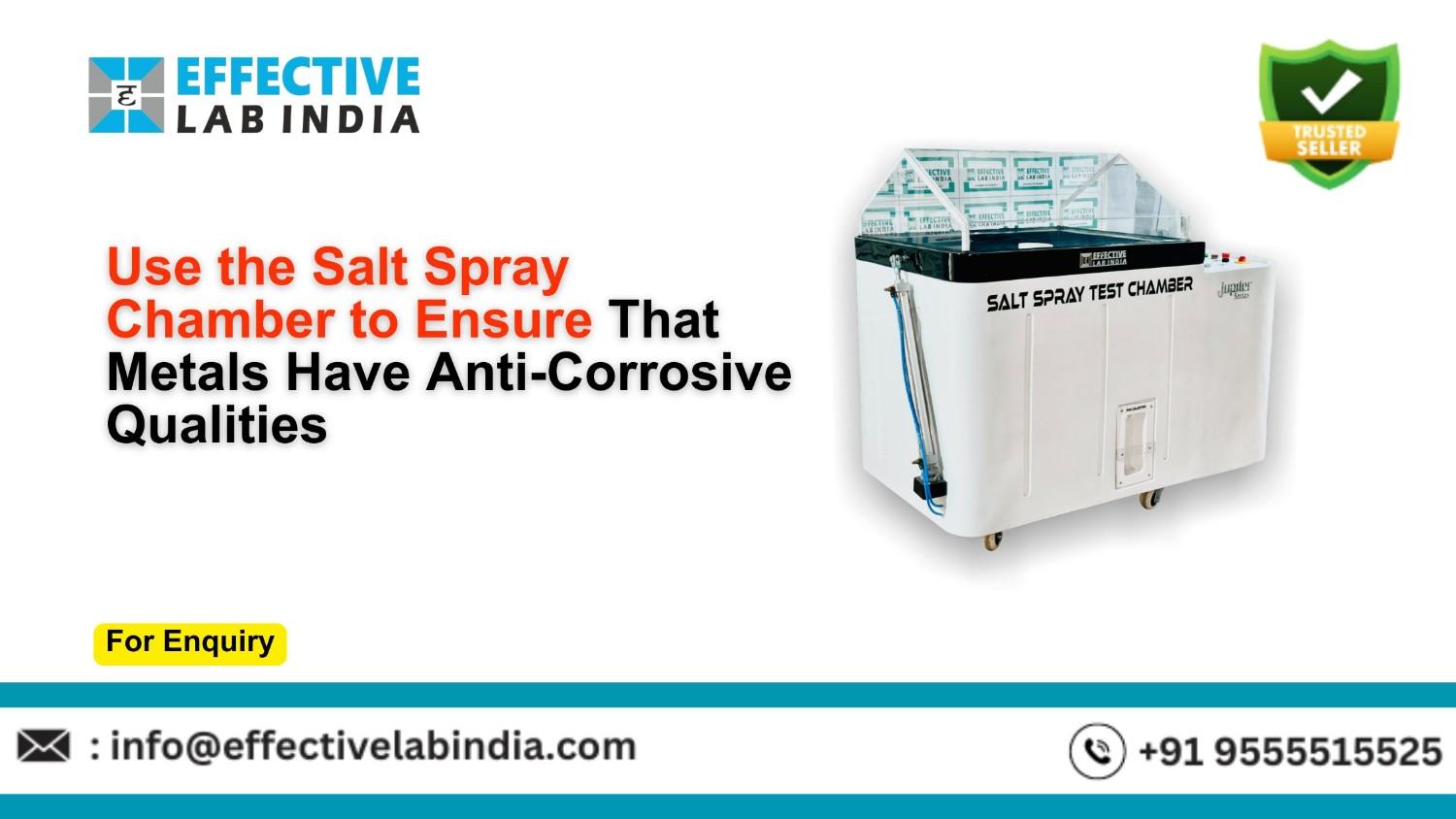
Use the Salt Spray Chamber to Ensure That Metals H
Updated at: 2024-09-30 07:08:22
Corrosion is an important threat for the long-term performance and reliability of metals, particular... Read More

What is the CASS CUM Salt Spray Chamber and How Do
Updated at: 2024-09-26 08:43:31
The CASS CUM salt spray chamber is a special type of laboratory equipment designed for corrosion tes... Read More

The Role of Cyclic Corrosion Chambers in Material
Updated at: 2024-09-26 06:48:30
Corrosion can silently compromise product integrity, leading to product failures, increased maintena... Read More

Salt Spray Test Chamber - The Perfect Tool to Prev
Updated at: 2024-09-23 12:45:27
The main component that has a major impact on the materials' and products' operating life and qualit... Read More

Salt Spray Test Chamber - The Ultimate Corrosion T
Updated at: 2024-09-21 06:18:04
Corrosion is a common issue in many industries, especially in metals and coatings encountered in ext... Read More

The Salt Spray Test Machine Features, Working, and
Updated at: 2024-09-14 08:02:12
Introduction to Salt Spray Test Machine In many different industries, corrosion is one of the most ... Read More

Understanding Salt Spray Chamber Working: Detailed
Updated at: 2024-09-11 07:53:19
When evaluating the corrosion resistance of materials, coatings, and components exposed to salty env... Read More
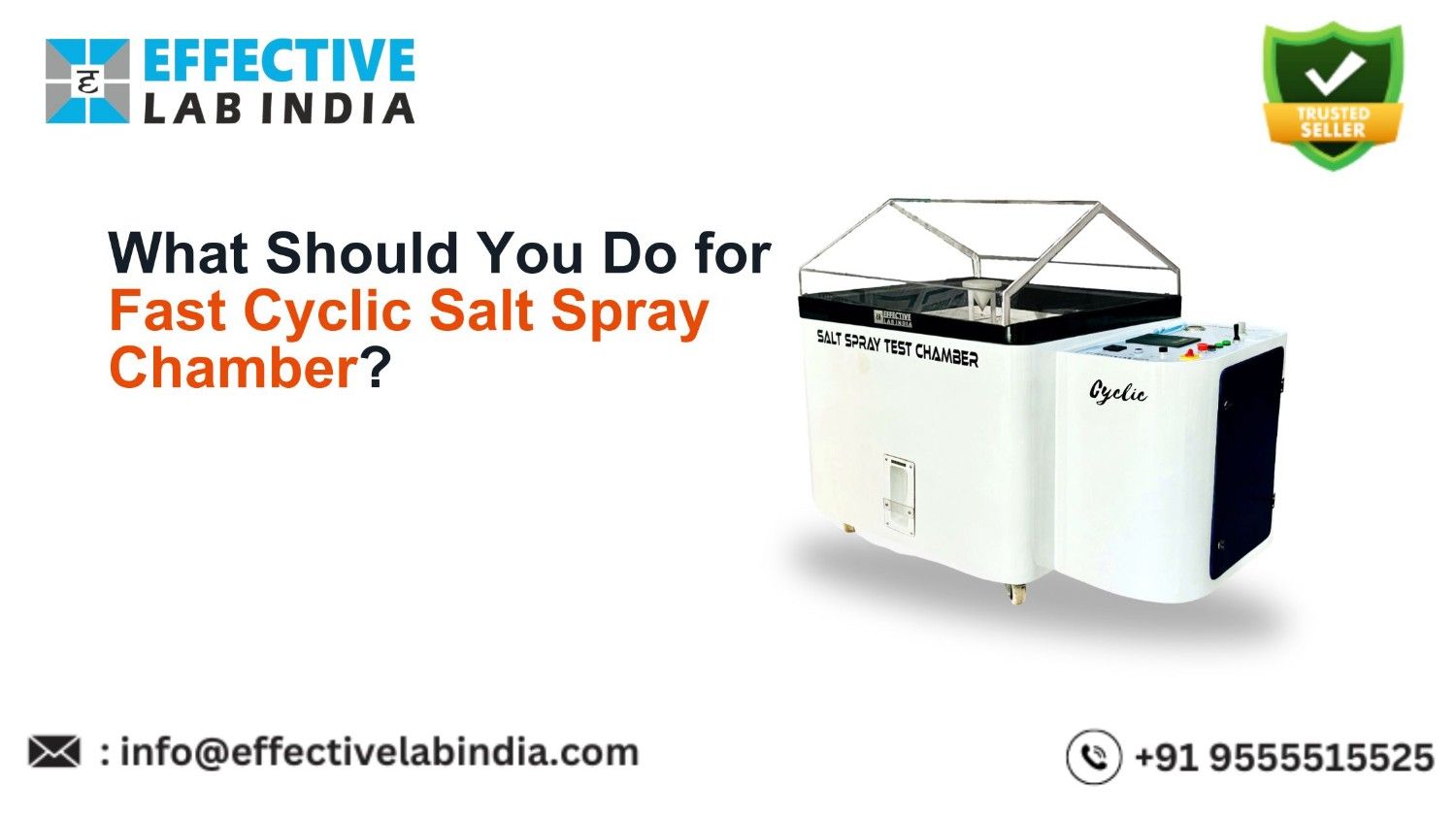
What Should You Do for Fast Cyclic Salt Spray Cham
Updated at: 2024-09-10 09:08:16
Cyclic salt spray chambers are a major equipment used by the automotive, aerospace, and construction... Read More

Comprehensive Guide to the Salt Spray Test Procedu
Updated at: 2024-09-06 12:32:53
When it comes to ensuring the durability of metal products and components, corrosion testing plays a... Read More

What is a 72-hour Salt Spray Test and 48-hour Salt
Updated at: 2024-09-04 06:52:04
The salt spray test is one of the most popular ways to evaluate corrosion resistance in the field of... Read More

A Comprehensive Guide to Salt Spray Chamber Manufa
Updated at: 2024-08-30 06:34:48
The corrosion testing equipment, mainly called salt spray chamber or salt spray mist chamber are imp... Read More

Different Test Methods for Testing Metal Using a S
Updated at: 2024-08-27 10:14:20
Metal testing is an essential procedure that protects the robustness, dependability, and durability ... Read More

Salt Spray Cabinets: The Best Testing Equipment fo
Updated at: 2024-08-22 09:41:47
Natural processes like corrosion may cause damage to metals and other materials, eventually resultin... Read More
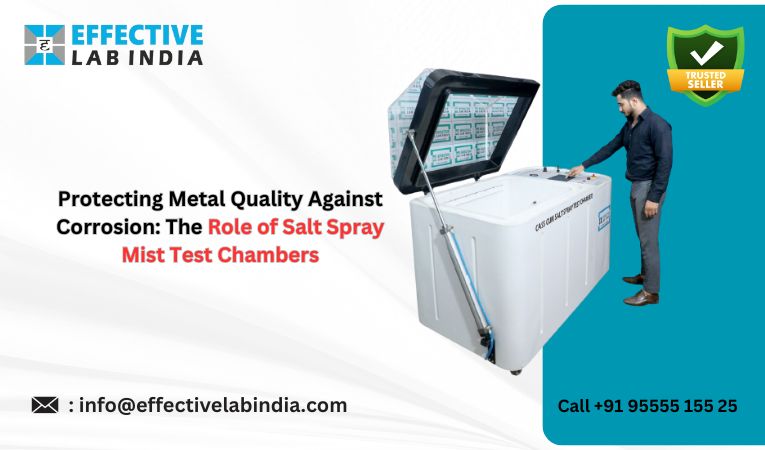
Protecting Metal Quality Against Corrosion: The Ro
Updated at: 2024-08-16 06:15:39
Metal surfaces meet a recurring problem with corrosion in a variety of industries. Exposure to extre... Read More

General Information on Salt Spray Test.
Updated at: 2024-03-30 09:24:53
A salt spray test is a laboratory test which is conducted to test the corrosion resistance propertie... Read More
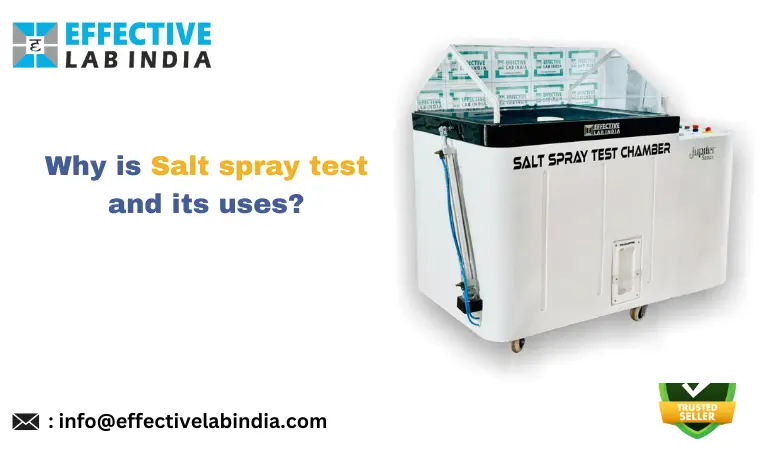
Why is salt spray test and its uses?
Updated at: 2024-03-28 11:38:28
The salt spray test is a scientific test that is conducted to test the corrosion resistance of diffe... Read More