by: Effective Lab India /salt spray test / Updated at: 2025-02-05 06:32:12
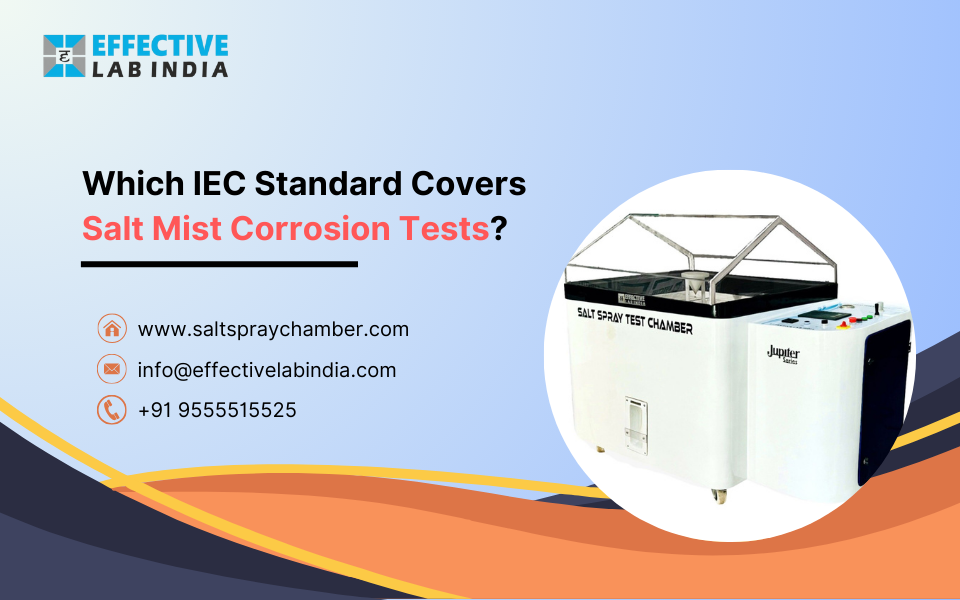
Salt mist corrosion tests are essential for assessing a material's or coating's resistance to corrosion. By simulating actual environmental conditions, these tests assist the industry in forecasting how long their products will last. Guidelines for these tests are provided by the International Electrotechnical Commission (IEC) under IEC 60068-2-11, commonly referred to as the Salt Mist Test Standard.
Overview of IEC 60068-2-11
The process for exposing materials to a regulated saline mist to evaluate their corrosion resistance is described in this standard by using a salt spray chamber. It is extensively utilized in the electronics, automotive, and aerospace sectors to guarantee the longevity and dependability of products.
Key Specifications of IEC 60068-2-11
- Test length: Usually between a few hours and several days.
- Composition of a saline solution: A solution containing a particular amount of sodium chloride.
- Conditions for testing: Spray rates, humidity, and temperature.
This standard is a crucial benchmark for manufacturers globally since it provides consistency and confidence in corrosion resistance examinations.
Decoding the IEC 68-2-27 Standard: Everything You Need to Know
As a component of the IEC 60068 series, the IEC 68-2-27 standard focuses on shock testing to assess the mechanical resilience of a product. This standard evaluates how well materials and components endure physical impacts such as drops, bumps, or vibrations, in contrast to corrosion tests.
Essential Components of IEC 68-2-27
- Shock waveform: Indicates the kind of force that was applied, like sawtooth or half-sine.
- Peak acceleration: Used to calculate the impact severity, measured in g-forces.
- Test cycles: Shocks are given repeatedly to mimic real-world situations.
In the automotive, aerospace, and electronics sectors to make sure their products can withstand abrupt impacts without experiencing a decline in performance. Maintaining product quality and dependability in dynamic environments requires an understanding of and adherence to IEC 68-2-27.
Exploring the IEC Standard for Corrosion Protection
The lifespan and functionality of materials can be greatly impacted by corrosion. The main recommendation for assessing corrosion resistance with salt spray or mist is the IEC 60068-2-11 standard. It is specially made to test base materials, surface treatments, and coatings in challenging conditions.
Advantages of Implementing IEC 60068-2-11
This standard gives manufacturers a methodical way to:
- Examine protective coatings to make sure they are corrosion-resistant.
- By simulating humid, salty circumstances, one may simulate real-world settings.
- Enhance the quality of the product: By determining the material's weak areas.
To make sure that manufacturers' goods are more dependable, long-lasting, and able to tolerate corrosive environments, adhere to IEC 60068-2-11. Because of this, IEC 60068-2-11 is a vital instrument in sectors including electronics, construction, and maritime.
A Comprehensive Guide to Salt Spray Test Standards
One of the most popular techniques for assessing a material's corrosion resistance is salt spray testing. These tests are governed by several international standards that guarantee dependability and consistency. Among the essential criteria are:
Important Standards for Salt Spray Testing
- IEC 60068-2-11: General salt mist tests are the main focus.
- ASTM B117: The most frequently accepted standard for evaluating salt spray is ASTM B117.
- ISO 9227: The neutral, acetic acid and copper-accelerated salt spray tests are specified in ISO 9227.
Typical Parameters for All Standards
There are particular instructions for each of these standards concerning:
- Preparing salt solutions.
- Configuration of the salt spray test chamber.
- Conditions and duration.
By adhering to these guidelines, producers can precisely forecast how resistant their materials and coatings will be to corrosion, guaranteeing end users long-lasting and high-quality products.
Effective Use of Salt Spray Testing for Corrosion Protection
A strong method for assessing corrosion resistance is salt spray testing, but how effectively it is carried out and understood determines how successful it is. Here's how to maximize this testing technique:
Tips for Effective Salt Spray Testing
- Recognize the Standards: Learn important guidelines such as ISO 9227, ASTM B117, or IEC 60068-2-11.
- Establish Reasonable Test Conditions: Make sure the test settings replicate the actual environment of the product.
- Get the samples ready correctly: To prevent inaccurate results, test specimens should be handled and cleaned following standard procedures.
- Keep an eye on the test conditions: To guarantee uniformity, monitor the saline solution, temperature, and humidity regularly.
- Examine the findings holistically: Accurate results require correlation with real-world performance.
Manufacturers can improve protective coatings, find material flaws, and produce corrosion-resistant materials that perform well in challenging conditions through salt spray testing.
Conclusion
For materials and products to be reliable and long-lasting in corrosive environments, salt spray testing and compliance with international standards such as IEC 60068-2-11 are essential. These guidelines offer a framework for attaining reliable and consistent outcomes, whether the goal is to strengthen coatings or protect metal surfaces. Manufacturers can improve product quality, gain consumer trust, and successfully satisfy industry standards by comprehending and putting these guidelines into practice.