by: Effective Lab India /salt spray test / Updated at: 2025-02-15 06:28:58
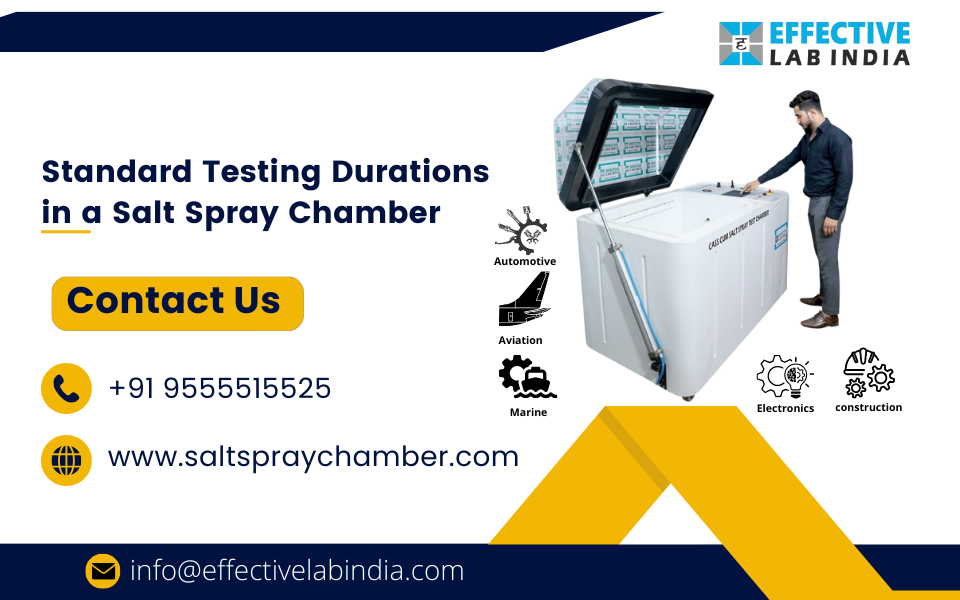
Introduction
In industries where metal components are used, corrosion resistance is an important factor in ensuring the life of the product. A widely used method for evaluating corrosion resistance is the salt spray chamber test. This method accelerates the corrosion process to determine how materials and coatings meet rigid environmental conditions. However, the test period in a corrosion test chamber varies depending on the industry standards. In this article, we will detect standard test periods, industry variation, and what factors affect these tests.
Understanding the Salt Spray Test
The salt spray fog test is a rapid corrosion test method that exposes the material in the fog of salt water inside a controlled chamber. The test evaluates the corrosion resistance of coatings, paints, and metals under simulated rigid conditions.
The Salt Spray Test Process
Preparation of samples - Test samples are cleaned and prepared according to standard guidelines.
Sample Placement - samples are arranged at an angle inside the salt spray chamber to ensure uniform exposure.
Spray cycleinization - a continuous fog of saline (usually 5% NaCl) is strewn to a controlled temperature (35 ° C or 95 ° F).
Monitoring and inspection - samples are inspected from time to time to assess corrosion effects.
Evaluation and reporting - Test results are compared to the industry's benchmark index.
Standard Testing Durations by Industry
Each industry follows specific guidelines for test periods in a salt spray chamber. The most common industry standards here are:
1. The automotive industry
Automakers extensively use salt spray samples on a large scale to evaluate the coatings and metal parts for rust resistance. Some large standards include:
ASTM B117 - 240 to 1000 hours, based on material.
ISO 9227 - usually 480 to 1000 hours.
SAE J2334- 80 to 200 cycles, copying conditions in the real world.
2. Aviation industry
Aviation manufacturers require strict testing due to extreme operating environments:
ASTM B117 - 168 to 720 hours for flight components.
MIL-STD-810- Up to 1000 hours for military quality materials.
Boeing and Airbus standard - 500 to 1000 hours adapted to specification.
3. Marine Industry
The marine environment is very corrosive, long-lasting test duration is required:
ASTM B117 - 500 to 2000 hours for ship components.
ISO 9227 - Marine constructions must have a minimum of 1000 hours.
4. The Electronics Sector
IEC 60068-2-52 circuit plates must be corrosion resistant for 144 to 672 hours for electronic components to be reliable.
MIL-STD-202: Military-class electronics up to 500 hours.
5. Infrastructure and construction
Galvanized steel and coatings are among the construction materials that undergo testing for extended corrosion resistance (480–1440 hours for ISO 12944-6-coatings).
ASTM G85: Industrial constructions, 1000–2500 hours.
Factors Affecting Testing Durations
Many factors affect the length of the salt spray test procedure including:
1. Material Type
Stainless steel and aluminum require longer exposure time.
Zinc-coated and painted surfaces can undergo smaller tests.
2. Coating Thickness
Rough coatings usually encounter long-term test periods.
3. Environmental Conditions
High temperatures and moisture levels can accelerate rust.
4. Industry-Specific Requirements
Military and aerospace industries impose stricter testing conditions.
Conclusion
The duration of testing in the salt spray test chamber varies considerably based on industry standards and material requirements. While some tests last for a few hundred hours, others expand over 2000 hours to simulate other extreme conditions. Understanding these variations helps manufacturers choose the right test procedures for their products.
FAQs (Salt Spray Chamber)
1. What is the purpose of a salt spray chamber?
A salt spray chamber is used to accelerate corrosion and evaluate the durability of coatings, metals, and materials in simulated environmental conditions.
2. How long does a standard salt spray test last?
Depending on the industry, standard testing durations range from 24 hours to over 2,000 hours.
3. What factors determine the duration of a salt spray test?
Material type, coating thickness, and industry-specific requirements influence test duration.
4. Is salt spray testing an accurate predictor of real-world corrosion?
While useful for comparative analysis, salt spray tests do not always replicate real-world environmental conditions precisely.
5. Can salt spray testing be customized for specific products?
Yes, many industries adjust testing parameters to suit their unique materials and environmental exposure expectations.